ALLOY 825 MATERIAL DATA SHEETS
Product Description
Available thicknesses for Alloy 825:
3/16" |
1/4" |
3/8" |
1/2" |
5/8" |
3/4" |
4.8mm |
6.3mm |
9.5mm |
12.7mm |
15.9mm |
19mm |
|
|||||
1" |
1 1/4" |
1 1/2" |
1 3/4" |
2" |
|
25.4mm |
31.8mm |
38.1mm |
44.5mm |
50.8mm |
|
Alloy 825 (UNS N08825) is an austenitic nickel-iron-chromium alloy with additions of molybdenum, copper and titanium. It was developed to provide exceptional corrosion resistance in both oxidizing and reducing environments. The alloy is resistant to chloride stress-corrosion cracking and pitting. The addition of titanium stabilizes Alloy 825 against sensitization in the as-welded condition making the alloy resistant to intergranular attack after exposure to temperatures in a range that would sensitize un-stabilized stainless steels. The fabrication of Alloy 825 is typical of nickel-base alloys, with material being readily formable and weldable by a variety of techniques.
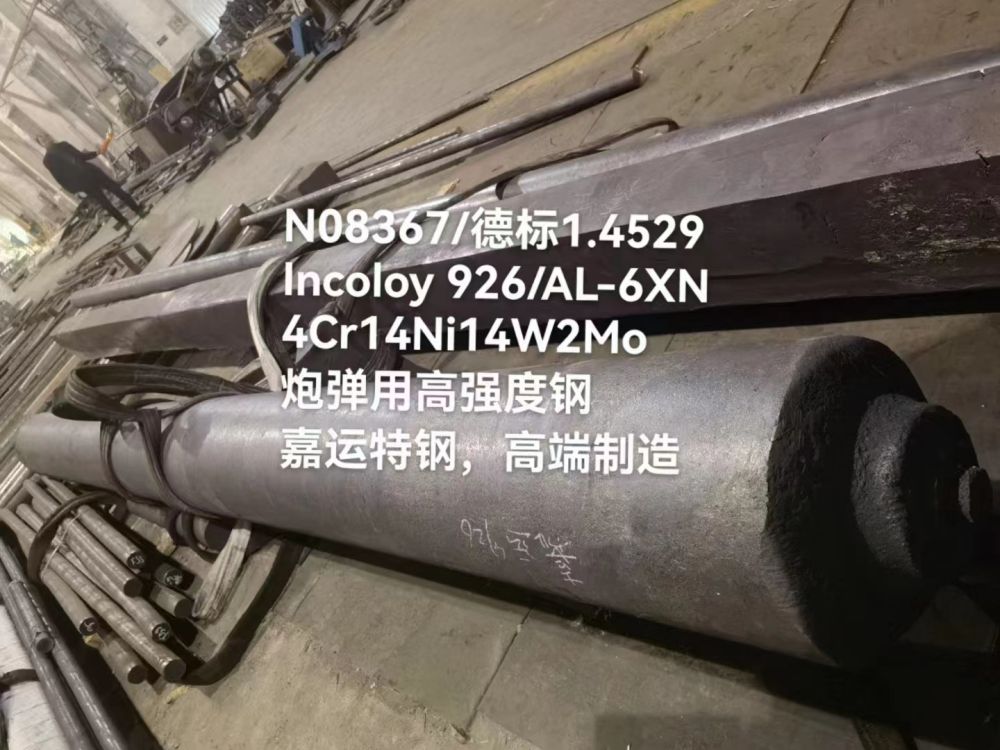
Specification Sheet
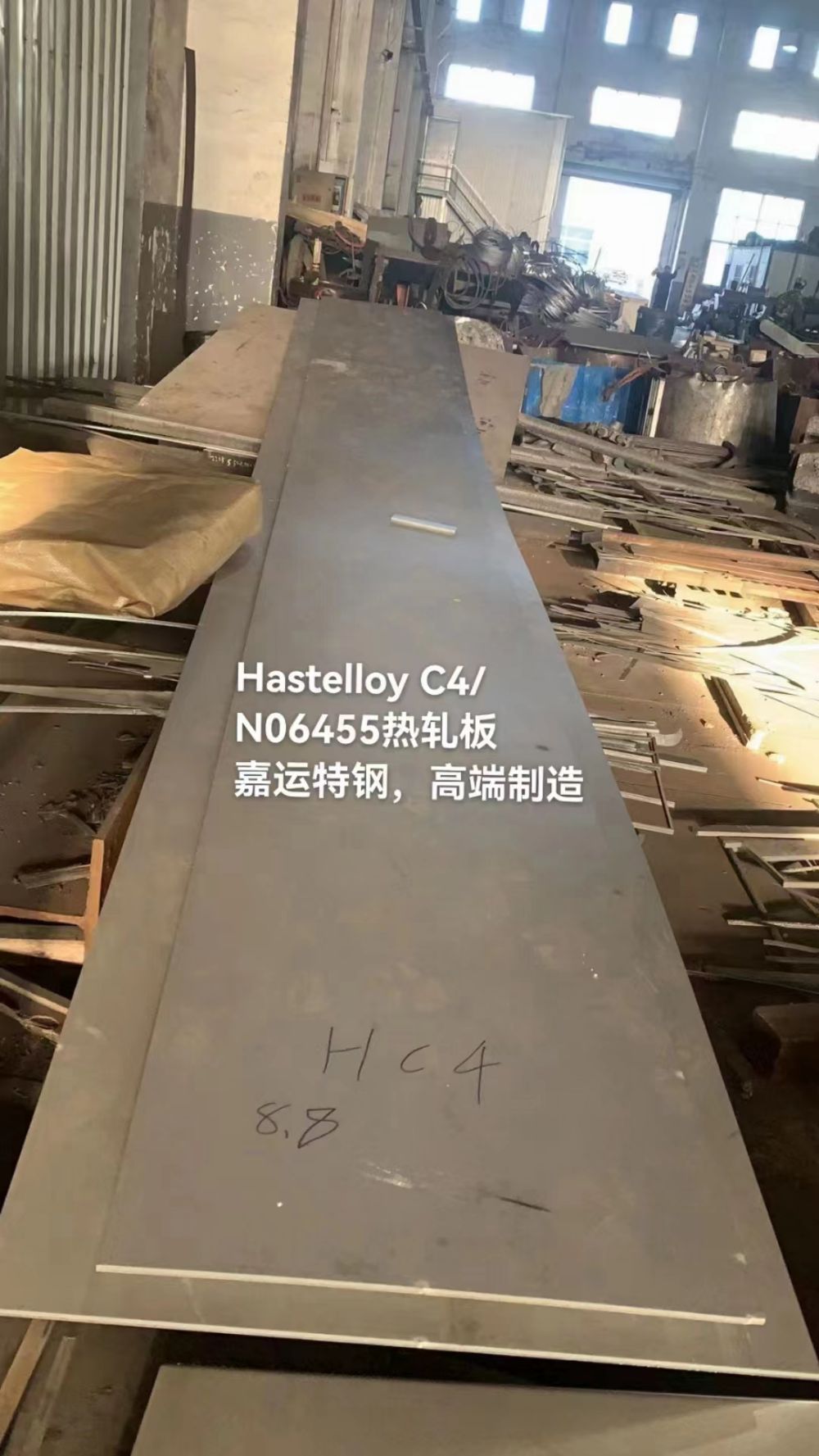
for Alloy 825 (UNS N08825)
W.Nr. 2.4858:
An Austenitic Nickel-Iron-Chromium Alloy Developed for Exceptional Corrosion Resistance In Both Oxidizing and Reducing Environments
● General Properties
● Applications
● Standards
● Chemical Analysis
● Physical Properties
● Mechanical Properties
● Corrosion Resistance
● Stress-Corrosion Cracking Resistance
● Pitting Resistance
● Crevice Corrosion Resistance
● Intergranular Corrosion Resistance
General Properties
Alloy 825 (UNS N08825) is an austenitic nickel-iron-chromium alloy with additions of molybdenum, copper and titanium. It was developed to provide exceptional resistance to numerous corrosive environments, both oxidizing and reducing.
The nickel content of Alloy 825 makes it resistant to chloride stress-corrosion cracking, and combined with molybdenum and copper, provides substantially improved corrosion resistance in reducing environments when compared to conventional austenitic stainless steels. The chromium and molybdenum content of Alloy 825 provides resistance to chloride pitting, as well as resistance to a variety of oxidizing atmospheres. The addition of titanium stabilizes the alloy against sensitization in the as-welded condition. This stabilization makes Alloy 825 resistant to intergranular attack after exposure in the temperature range which would typically sensitize un-stabilized stainless steels.
Alloy 825 is resistant to corrosion in a wide variety of process environments including sulfuric, sulfurous, phosphoric, nitric, hydrofluoric and organic acids and alkalis such as sodium or potassium hydroxide, and acidic chloride solutions.
The fabrication of Alloy 825 is typical of nickel-base alloys, with material readily formable and weldable by a variety of techniques.
Applications
● Air Pollution Control
● Scrubbers
● Chemical Processing Equipment
● Acids
● Alkalis
● Food Process Equipment
● Nuclear
● Fuel Reprocessing
● Fuel Element Dissolvers
● Waste Handling
● Offshore Oil and Gas Production
● Seawater Heat Exchangers
● Piping Systems
● Sour Gas Components
● Ore Processing
● Copper Refining Equipment
● Petroleum Refining
● Air-cooled Heat Exchangers
● Steel Pickling Equipment
● Heating Coils
● Tanks
● Crates
● Baskets
● Waste Disposal
● Injection Well Piping Systems
Standards
ASTM..................B 424
ASME..................SB 424
Chemical Analysis
Typical Values (Weight %)
Nickel |
38.0 min.–46.0 max. |
Iron |
22.0 min. |
Chromium |
19.5 min.–23.5 max. |
Molybdenum |
2.5 min.–3.5 max. |
Molybdenum |
8.0 min.-10.0 max. |
Copper |
1.5 min.–3.0 max. |
Titanium |
0.6 min.–1.2 max. |
Carbon |
0.05 max. |
Niobium (plus Tantalum) |
3.15 min.-4.15 max. |
Titanium |
0.40 |
Carbon |
0.10 |
Manganese |
1.00 max. |
Sulfur |
0.03 max. |
Silicon |
0.5 max. |
Aluminium |
0.2 max. |
|
Physical Properties
Density
0.294 lbs/in3
8.14 g/cm3
Specific Heat
0.105 BTU/lb-°F
440 J/kg-°K
Modulus of Elasticity
28.3 psi x 106 (100°F)
196 MPa (38°C)
Magnetic Permeability
1.005 Oersted (μ at 200H)
Thermal Conductivity
76.8 BTU/hr/ft2/ft-°F (78°F)
11.3 W/m-°K (26°C)
Melting Range
2500 – 2550°F
1370 – 1400°C
Electrical Resistivity
678 Ohm circ mil/ft (78°F)
1.13 μ cm (26°C)
Linear Coefficient of Thermal Expansion
7.8 x 10-6 in / in°F (200°F)
4 m / m°C (93°F)
Mechanical Properties
Typical Room Temperature Mechanical Properties, Mill Annealed
Yield Strength 0.2% Offset |
Ultimate Tensile Strength |
Elongation in 2 in. |
Hardness |
||
psi (min.) |
(MPa) |
psi (min.) |
(MPa) |
% (min.) |
Rockwell B |
49,000 |
338 |
96,000 |
662 |
45 |
135-165 |
Alloy 825 has good mechanical properties from cryogenic to moderately high temperatures. Exposure to temperatures above 1000°F (540°C) can result in changes to the microstructure that will significantly lower ductility and impact strength. For that reason, Alloy 825 should not be utilized at temperatures where creep-rupture properties are design factors. The alloy can be strengthened substantially by cold work. Alloy 825 has good impact strength at room temperature, and retains it’s strength at cryogenic temperatures.
Table 6 - Charpy Keyhole Impact Strength of Plate
Temperature |
Orientation |
Impact Strength* |
||
°F |
°C |
|
ft-lb |
J |
Room |
Room |
Longitudinal |
79.0 |
107 |
Room |
Room |
Transverse |
83.0 |
113 |
-110 |
-43 |
Longitudinal |
78.0 |
106 |
-110 |
-43 |
Transverse |
78.5 |
106 |
-320 |
-196 |
Longitudinal |
67.0 |
91 |
-320 |
-196 |
Transverse |
71.5 |
97 |
-423 |
-253 |
Longitudinal |
68.0 |
92 |
-423 |
-253 |
Transverse |
68.0 |
92 |
Corrosion Resistance
The most outstanding attribute of Alloy 825 is its excellent corrosion resistance. In both oxidizing and reducing environments, the alloy resists general corrosion, pitting, crevice corrosion, intergranular corrosion and chloride stress-corrosion cracking.
Resistance to Laboratory Sulfuric Acid Solutions
Alloy |
Corrosion Rate in Boiling Laboratory Sulfuric Acid Solution Mils/Year (mm/a) |
||
10% |
40% |
50% |
|
316 |
636 (16.2) |
>1000 (>25) |
>1000 (>25) |
825 |
20 (0.5) |
11 (0.28) |
20 (0.5) |
625 |
20 (0.5) |
Not Tested |
17 (0.4) |
Stress-Corrosion Cracking Resistance
The high nickel content of Alloy 825 provides superb resistance to chloride stress-corrosion cracking. However, in the extremely severe boiling magnesium chloride test, the alloy will crack after long exposure in a percentage of samples. Alloy 825 performs much better in less severe laboratory tests. The following table summarizes the alloy's performance.
Resistance to Chloride Stress Corrosion Cracking
Alloy Tested as U-Bend Samples |
||||
Test Solution |
Alloy 316 |
SSC-6MO |
Alloy 825 |
Alloy 625 |
42% Magnesium Chloride (Boiling) |
Fail |
Mixed |
Mixed |
Resist |
33% Lithium Chloride (Boiling) |
Fail |
Resist |
Resist |
Resist |
26% Sodium Chloride (Boiling) |
Fail |
Resist |
Resist |
Resist |
Mixed – A portion of the samples tested failed in the 2000 hours of test. This is an indication of a high level of resistance.
Pitting Resistance
The chromium and molybdenum content of Alloy 825 provides a high level of resistance to chloride pitting. For this reason the alloy can be utilized in high chloride environments such as seawater. It can be used primarily in applications where some pitting can be tolerated. It is superior to conventional stainless steels such as 316L, however, in seawater applications Alloy 825 does not provide the same levels of resistance as SSC-6MO (UNS N08367) or Alloy 625 (UNS N06625).
Crevice Corrosion Resistance
Resistance to Chloride Pitting and Crevice Corrosion
Alloy |
Temperature of Onset at Crevice Corrosion Attack* °F (°C) |
316 |
27 (-2.5) |
825 |
32 (0.0) |
6MO |
113 (45.0) |
625 |
113 (45.0) |
*ASTM Procedure G-48, 10% Ferric Chloride
Intergranular Corrosion Resistance
Alloy |
Boiling 65% Nitric Acid ASTM Procedure A 262 Practice C |
Boiling 65% Nitric Acid ASTM Procedure A 262 Practice B |
316 |
34 (.85) |
36 (.91) |
316L |
18 (.47) |
26 (.66) |
825 |
12 (.30) |
1 (.03) |
SSC-6MO |
30 (.76) |
19 (.48) |
625 |
37 (.94) |
Not Tested |